Project description
This project deals with the simulation and experimental validation of eigenstresses in laser- generated composite materials. These materials are used as wear-resistant coatings protecting metallic surfaces against abrasion, erosion or corrosion. Laser dispersion is the primary process used in this project, where working surfaces of already manufactured parts are coated by adding tungsten carbide powder into the melt pool of a base material. The coating extends the part's lifetime due to the outstanding material characteristics of the locally produced metal matrix composite (MMC). Eigenstresses, which are the residual stresses left in the MMC material after the coating process, shall be investigated and predicted within the framework of this project.
The first figure below show the processing method in (a) and the final product in (c). The image in (b) and in the second figure illustrate the structure of the material used in the coating process.
The aim is to find ways for optimizing the stress distribution by numerical investigations. For instance, the influence of processing conditions on the residual stresses may be analyzed to optimize the processing method. The challenging thermo-mechanical simulations needed for the predictions will be realized in dedicated multi-physical reduced order models (ROM). Further, data-driven techniques will assist in the exploitation of the simulation results. For instance, data-driven models accounting for temperature, particle content and distribution will be supplied by the ROM. The project is divided into multiple stages and tackled with the help of two partners: Bremen Institute for Applied Beam Technology (BIAS) and Heinz Maier-Leibnitz Zentrum (MLZ) in Garching. As illustrated in the overview below, our part can be summarised within two key aspects modeling and simulation, while BIAS will develop the underlying technical process and MLZ will perform neutron diffraction measurements that will help in the calibration of the simulation and for experimental validation.
Data Analytics in Engineering is embedded into the Cluster of Excellence Data-Integrated Simulation Science (SimTech, EXC-2075 - DFG project number 390740016). Efficient simulations of various microstructures is done in close collaboration with PN3A-2 and there are plans to incorporate uncertainties by joining effort with PN3-1. In addition, the funding line of the project (AiF/IGF, i.e. BMWi) involves the close interaction with industrial partners.
Project information
Project title | Simulation and experimental validation of residual stresses in laser-generated composite materials |
Project leader | Felix Fritzen |
Project duration | July 2020 - December 2022 |
Project number | PN 3 A-3 |
Publications PN 3 A-3
2025
- F. Fritzen, J. Herb, and S. Sharba, “Thermo-plastic Nonuniform Transformation Field Analysis for eigenstress analysis of materials undergoing laser melt injection,” Computer Methods in Applied Mechanics and Engineering, vol. 433, p. 117487, Jan. 2025, doi: 10.1016/j.cma.2024.117487.
2023
- S. Sharba, J. Herb, and F. Fritzen, “Reduced order homogenization of thermoelastic materials with strong temperature dependence and comparison to a machine-learned model,” Archive of Applied Mechanics, vol. 93, Art. no. 7, Jul. 2023, doi: 10.1007/s00419-023-02411-6.
Funding
The IGF-Project no.: 21.079 N / DVS-No.: 06.3341 of the “Forschungsvereinigung Schweißen und verwandte Verfahren e.V.” of the German Welding Society (DVS), Aachener Str. 172, 40223 Düsseldorf, Germany, was funded by the Federal Ministry for Economic Affairs and Energy (BMWi) via the German Federation of Industrial Research Associations (AiF) in accordance with the policy to support the Industrial Collective Research (IGF) on the orders of the German Bundestag.
Funded by the German Research Foundation (DFG) 390740016 / EXC-2075.
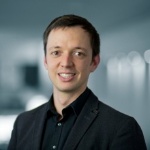
Felix Fritzen
Prof. Dr.-Ing. Dipl.-Math. techn.Data Analytics in Engineering